Commercial air conditioner systems are the backbone of indoor climate control for offices, retail spaces, industrial facilities, and multi-use buildings.
These systems operate for extended hours, often in demanding conditions, and are responsible for maintaining consistent comfort across large spaces.
Unlike residential units, commercial ACs are complex, high-capacity machines that require structured and timely maintenance to perform efficiently.
Without a regular service schedule, commercial air conditioners can experience a drop in performance, increased energy consumption, frequent breakdowns, and shortened lifespan.
According to the U.S. Department of Energy, routine maintenance can cut energy use by 15% or more significant savings for businesses with tight operational budgets.
Moreover, proactive servicing helps avoid downtime, improves air quality, and ensures consistent indoor temperatures, which directly impact employee productivity and customer experience.
Every building has different needs, but the foundation of air conditioning efficiency lies in following a dependable, data-driven maintenance routine.
It’s not just about fixing problems when they arise—it’s about preventing them in the first place through scheduled inspections, cleanings, testing, and performance tracking.
Commercial Air Conditioner Service Schedule to Maximize Efficiency
In this guide, we will explain a complete commercial air conditioner service schedule to help you maximize efficiency and reduce long-term operational costs.
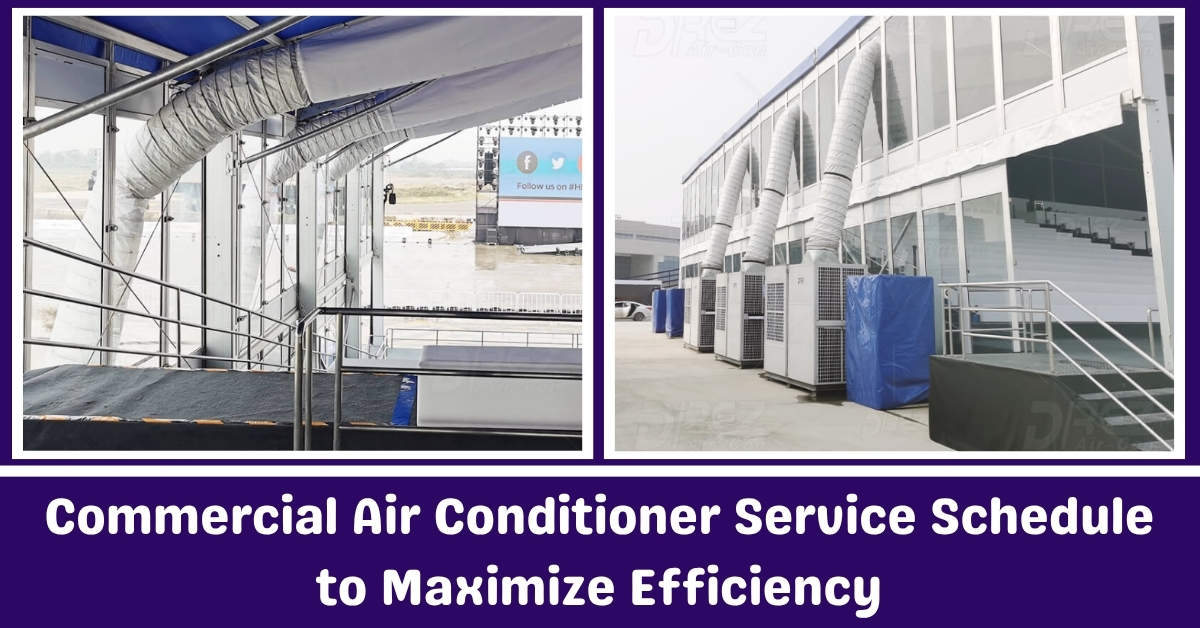
Why Consistent AC Service Scheduling Matters
Consistency in servicing a commercial air conditioner is essential for operational efficiency, cost control, and system longevity. A commercial HVAC system often runs for extended hours and covers large spaces, making it subject to wear and tear much faster than residential units.
If ignored, this wear can reduce efficiency by 15–30%, increase energy consumption, and raise the risk of system failures. Regular servicing ensures that parts are clean, components are functioning correctly, and small issues are caught before becoming costly repairs.
Routine maintenance also reduces energy waste. Dirty filters, blocked coils, and leaking ducts force the system to work harder, raising utility bills significantly.
In a commercial building, where HVAC often accounts for 30–50% of total energy use, even minor efficiency improvements can save thousands of dollars annually.
Furthermore, sticking to a service schedule can increase the lifespan of your system by several years, reducing capital expenditure on premature replacements.
Overall, planned maintenance is not optional—it’s a necessary part of facility management that directly impacts the bottom line.
Service Schedule Overview
Having a clear, documented service schedule allows facility managers and technicians to stay proactive rather than reactive.
A commercial air conditioner requires attention on multiple timelines monthly, quarterly, biannually, annually, and on-demand.
These intervals target different components and functions of the system. Monthly tasks often involve basic inspections and filter changes.
Quarterly services go deeper, focusing on coils, refrigerant levels, and airflow checks. Biannual checks are usually scheduled before seasonal peaks to prepare the system for high usage.
Annual inspections take a comprehensive approach, checking all electrical, mechanical, and performance parameters. Finally, on-demand servicing is needed when performance issues or breakdowns occur.
By organizing maintenance around these intervals, buildings can ensure consistent comfort, reduce downtime, and achieve optimal system performance year-round.
This structure also simplifies budgeting and planning, allowing teams to allocate resources and technician hours efficiently.
Monthly Service Tasks (In-House or Contracted)
Monthly maintenance is mostly preventive and often handled by in-house facility staff or entry-level HVAC support. The most critical task at this frequency is checking and replacing air filters.
Dirty filters reduce airflow, cause the system to work harder, and can lead to overheating or frozen coils.
In most commercial environments, filters should be replaced every 30–60 days, though dusty or high-traffic areas may require more frequent changes.
Another key monthly task is visual inspection. This includes checking vents, registers, and return ducts for obstructions. Items like furniture, paper, or storage boxes should not block air circulation.
Outdoor units should be free from debris such as leaves, dust, or plastic.
It’s also important to confirm that thermostat settings align with current operating hours, occupancy levels, and seasonal temperature changes. Even a two-degree difference in setpoint temperature can impact energy bills significantly.
These monthly checks are quick but essential. Skipping them leads to compounding issues that show up in quarterly or annual inspections as more severe problems.
Quarterly Service Tasks (Recommended by HVAC Technicians)
Quarterly maintenance should be handled by qualified HVAC technicians. These visits go beyond the surface and involve system performance checks, coil cleaning, and refrigerant monitoring.
One of the main tasks is cleaning the evaporator and condenser coils.
When coils are dirty, heat transfer becomes inefficient, which makes the compressor run longer and consume more power. Coil cleaning improves airflow and cooling capacity, which can directly reduce energy costs.
Technicians should also check refrigerant pressure levels to ensure the system is properly charged.
Low refrigerant levels can indicate a leak, while overcharging can cause compressor damage. Either condition affects cooling efficiency and should be addressed immediately.
Additionally, drain lines and pans need to be inspected and cleaned to prevent mold growth or overflow issues that can cause water damage.
Another important task is checking fan motors, belts, and overall airflow. A worn fan belt or misaligned blower can reduce airflow and make the system less effective, especially in larger zones.
Using an anemometer to measure airspeed at vents is a good practice for confirming proper distribution.
Biannual Service Tasks (Pre-Season Maintenance)
Biannual servicing should be scheduled before summer and winter, the two periods when HVAC systems face peak demand.
This level of maintenance involves more in-depth inspection and is often bundled as pre-season preparation. It includes a full mechanical tune-up of key components such as compressors, contactors, and capacitors.
Lubrication of moving parts is essential to prevent mechanical friction, which can shorten component lifespan.
A full duct inspection should also be included in biannual service. Ducts may develop leaks, gaps, or loose connections over time, which leads to significant energy losses.
Leaky ductwork can reduce overall efficiency by up to 30%. Sealing or repairing problem areas helps improve air delivery and system performance.
Thermostats must be calibrated to ensure the displayed temperature matches the actual room temperature. Even minor discrepancies can result in systems running longer than necessary.
Modern commercial systems often include programmable thermostats or building automation systems (BAS), which should be updated or reconfigured based on occupancy and load changes.
Annual Service Tasks (Full Diagnostic)
Annual maintenance is the most comprehensive and typically requires a certified commercial HVAC professional.
It includes electrical testing, motor diagnostics, system performance benchmarking, and a full review of the unit’s mechanical health.
Technicians will perform continuity tests on electrical components, inspect wiring for wear, and test circuit boards for signs of failure or overheating.
One of the most important aspects of annual servicing is testing system efficiency. This involves checking the cooling output relative to energy input, usually measured in BTU/hr and kilowatt-hours.
Results are compared against baseline standards from organizations such as ASHRAE or ENERGY STAR.
If performance metrics fall below acceptable ranges, it may be time to upgrade components or recalibrate system controls.
The insulation on refrigerant lines should also be checked annually. Damaged or missing insulation allows energy losses and can lead to line freezing.
Outdoor units are particularly vulnerable to UV exposure, which deteriorates insulation faster.
This inspection also involves reviewing maintenance records to identify recurring issues or signs of system aging.
These insights help plan long-term replacements or upgrades, avoiding unexpected failures during critical business periods.
On-Demand Service Tasks (As Needed)
Even with the best maintenance schedules, unexpected issues can occur. That’s where on-demand servicing comes in.
These tasks are reactive and triggered by system alerts, performance drops, or physical signs like unusual noise, temperature imbalances, or leaking water.
Common reasons for emergency servicing include compressor failures, sensor malfunctions, or refrigerant leaks.
Modern commercial systems may have diagnostic software or remote monitoring tools that flag errors in real time.
When this happens, technicians need to respond quickly, identify the issue, and resolve it before it affects building occupants or processes.
Software and firmware updates should also be conducted as needed to fix bugs or improve system compatibility with newer control technologies.
In high-priority cases, component replacements such as fan motors, valves, or thermostats may be necessary. It’s important to keep essential parts in stock to reduce downtime during these interventions.
Keeping a relationship with a responsive service provider ensures faster turnaround during unplanned maintenance events.
Metrics to Monitor After Each Service
To validate the effectiveness of your maintenance program, track performance metrics after every service. Start by recording indoor temperature stability and energy usage (kWh) during occupied hours.
Compare these figures before and after maintenance to spot improvements or ongoing inefficiencies.
Another key metric is system runtime. If the system is cycling on and off too frequently, it could signal an underlying issue with sensors, load calculations, or refrigerant levels.
Likewise, track the number of service calls, types of repairs, and cost per repair. These data points help identify trends, such as components that fail repeatedly or seasonal performance drops.
Use these metrics to guide future decisions about upgrades, technician scheduling, and budget allocation. Regularly reviewing performance data ensures your system is improving not just being serviced out of routine.
Common Warning Signs That You Need Immediate Service
Some signs should never be ignored. These include unusually high energy bills, loud or unusual noises from the HVAC unit, inconsistent cooling across rooms or zones, water leakage, and frequent cycling.
High humidity levels indoors or the presence of moldy odors can also indicate issues with drainage or air handling.
A drop in thermostat responsiveness or visible ice on the evaporator coils are additional signs that immediate service is needed. These symptoms often point to refrigerant or airflow problems and can lead to major damage if left unaddressed.
If these signs appear shortly after a scheduled maintenance visit, it may indicate that some issues were missed or have developed quickly.
Addressing them early prevents minor issues from escalating into full-system failures.
Tips to Make Your Service Schedule Work
To make your service schedule effective, consistency and documentation are key. Start by creating a maintenance calendar with specific dates for each service level monthly, quarterly, biannual, and annual.
Assign these tasks to specific team members or an HVAC contractor to ensure accountability.
Keep detailed service logs for every visit. These should include work performed, parts replaced, technician notes, and follow-up recommendations.
Over time, these records help identify performance trends and inform capital planning for replacements or upgrades.
Use a computerized maintenance management system (CMMS) or building automation software to automate reminders, track system data, and centralize documentation.
This technology minimizes human error and allows faster response to performance issues. Lastly, train in-house staff to recognize basic warning signs so they can escalate problems early.
By combining a structured plan with trained personnel and proper tools, your commercial air conditioning system can operate at peak efficiency year-round with fewer breakdowns and lower costs.
Conlusion
A well-structured service schedule is essential to keep your commercial air conditioner running efficiently, reliably, and cost-effectively.
Regular maintenance is not just about avoiding breakdowns it directly impacts energy consumption, system lifespan, and the comfort of your facility.
By following a routine that includes monthly checks, quarterly performance reviews, biannual tune-ups, annual diagnostics, and timely on-demand servicing, you ensure that small issues are caught early before they evolve into major, expensive problems.
Consistent servicing improves airflow, ensures proper refrigerant levels, keeps electrical components safe, and maintains optimal indoor climate control.
It also provides valuable performance data that can be used to plan upgrades, budget maintenance expenses, and predict system lifespan.
For building managers and business owners, the takeaway is simple: don’t wait for your AC system to fail. Create a clear service calendar, use trained professionals, track key performance metrics, and make preventive maintenance a priority.
In the long run, a proactive approach saves money, reduces operational stress, and ensures your business environment stays comfortable and productive all year round.