Engineering cooling unit systems play a critical role in maintaining stable operating temperatures across a wide range of industrial and technical environments.
Whether installed in CNC machinery, data centers, control panels, or manufacturing equipment, these units are designed to prevent overheating, reduce thermal stress, and ensure equipment longevity.
When a cooling unit begins to fail, the consequences can be immediate and costly ranging from unscheduled downtime to irreversible damage of sensitive components.
Unlike other system issues that may be gradual or cosmetic, cooling failures often escalate quickly if warning signs are missed.
Identifying those early red flags isn’t just good practice it’s essential for operational safety and equipment performance.
From rising temperatures and coolant leaks to irregular sensor data and increased power draw, these symptoms tell a story about what’s going wrong beneath the surface.
For maintenance engineers, facility managers, and technical operators, being able to interpret these signs early can prevent large-scale failure, reduce repair costs, and help maintain production schedules without disruption.
Engineering cooling unit failure signs and what they mean
In this guide, we will explain the key failure signs of engineering cooling units and what each of them means in practical terms.
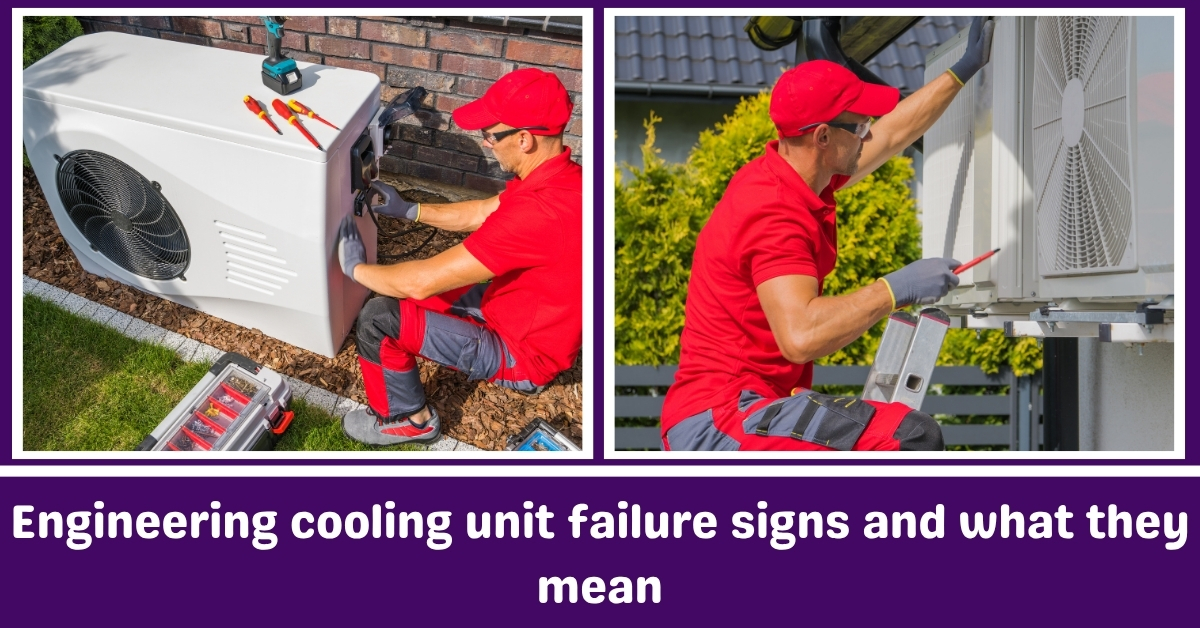
Why Cooling Unit Performance Matters
Engineering cooling units are essential for regulating temperature in high-demand environments such as industrial machinery, server rooms, and manufacturing systems.
These units ensure that internal components do not exceed safe thermal limits, which, if breached, can lead to overheating, equipment malfunction, or permanent damage.
The performance of these cooling units directly affects the efficiency, reliability, and lifespan of the systems they support.
Poor cooling leads to increased thermal stress on electronics and mechanical components, resulting in wear and tear, unplanned downtime, and costly repairs.
Continuous optimal performance of a cooling unit also contributes to energy efficiency, minimizing excessive power draw and operational costs.
Therefore, maintaining cooling units and monitoring their performance is not optional it is a core part of sustaining system health and operational continuity.
Rising Operating Temperatures
One of the most straightforward signs of cooling unit failure is a steady increase in system temperature. If equipment begins running hotter than normal, it’s a strong indicator that the cooling unit is no longer performing effectively.
This could be due to reduced coolant flow, fan speed issues, or clogged ventilation pathways. Rising temperatures put pressure on critical components, which can cause thermal expansion, reduced conductivity, and ultimately, system shutdown.
Monitoring temperature sensors regularly and setting thresholds for alarms can help detect this early.
Consistent readings above the recommended operating temperature range should trigger immediate inspection and corrective action.
Fluctuating Temperature Readings
Temperature fluctuations that occur without corresponding load changes point to an inconsistency in cooling performance. These irregular readings often stem from malfunctioning sensors, unstable airflow, or failing fans.
Fluctuating temperatures are harmful because they create a thermal cycling effect, where components are repeatedly stressed by changes in heat.
This accelerates fatigue and can cause solder joints or internal circuits to fail prematurely. These fluctuations are particularly problematic in electronics and high-precision machinery.
If your monitoring system detects such variations, it’s important to inspect the cooling loop, recalibrate temperature sensors, and verify that all fans and airflow paths are functioning as designed.
Unusual Noise from Equipment
Mechanical noise such as grinding, rattling, or high-pitched whines is a clear indication that a cooling unit’s moving components are under stress.
Fans and pumps, which operate continuously, are prone to wear over time. When bearings become loose or impellers become misaligned, noise levels increase.
This noise is not just an annoyance it’s a signal that a component may soon fail. In most cases, replacing bearings or aligning parts early is more cost-effective than dealing with a failed system later.
Operators should regularly listen for changes in noise profiles and address anomalies immediately, as continued operation under such conditions can quickly escalate to full breakdowns.
Frequent System Shutdowns
Unscheduled or frequent shutdowns during operation, especially under normal load conditions, often indicate that thermal protection mechanisms are being triggered.
Most modern engineering systems are built with sensors and auto-shutdown features that activate when the temperature exceeds safe limits.
These shutdowns are safety responses designed to prevent permanent damage.
However, their frequency points to an underlying problem in the cooling unit. It may be due to insufficient heat dissipation, blocked airflow, or degraded thermal transfer mediums.
Identifying the root cause of these shutdowns is essential, and the first step is to review system logs and cooling system metrics to detect irregularities.
Increased Energy Consumption
If your system’s energy usage spikes without a corresponding increase in workload, this could be a sign that the cooling unit is compensating for reduced efficiency.
When fans are clogged, filters are dirty, or coolant is insufficient, the system works harder to maintain acceptable temperatures, which leads to more power consumption.
This not only increases operational costs but also places unnecessary strain on the electrical infrastructure.
Routine monitoring of energy usage against equipment specifications allows facility managers to detect when cooling performance begins to degrade.
Investigating unusual power draw and performing timely maintenance can restore energy efficiency and prevent further wear.
Coolant Leaks
Coolant is the primary medium used in many cooling units to transfer heat away from components. A leak in the system reduces the available coolant volume, directly diminishing the unit’s ability to manage heat.
Leaks can occur due to worn gaskets, corroded tubing, or poor connections. Visual inspections may reveal puddles near the base of units, moisture around joints, or unexpectedly low coolant levels in reservoirs.
In some cases, coolant may evaporate quickly, making leaks harder to spot. Using leak detection fluids or pressure testing methods can help confirm issues.
Once identified, it’s critical to repair the leak and restore proper coolant levels before system damage occurs.
Dust and Blockages
Air-cooled systems rely heavily on unobstructed airflow to dissipate heat effectively. Dust accumulation on filters, vents, and coils restricts this flow and lowers cooling efficiency.
When airflow is limited, heat builds up, and components may begin to overheat. Dust also acts as an insulator on heat exchangers, making it harder for them to release heat into the surrounding environment.
Over time, this causes the cooling system to work harder, increasing wear and power usage.
Regular cleaning of intake filters, blower fans, and coil surfaces is one of the simplest yet most effective ways to maintain optimal performance. In industrial environments, this may need to be done weekly or even daily, depending on air quality.
Corroded Components
Corrosion within a cooling unit typically affects coils, fittings, and metal piping. It reduces the effectiveness of heat transfer and increases the risk of leaks or mechanical failure.
Corrosion can be caused by environmental factors like humidity, chemical exposure, or galvanic reactions between dissimilar metals. Visible signs include rust, discoloration, or flaking on metallic surfaces.
Over time, corrosion degrades the structural integrity of components, leading to cracks or perforations.
Addressing this involves replacing affected parts and using corrosion-resistant materials, such as stainless steel or coated metals.
Environmental control, such as dehumidification and proper ventilation, can also help prevent corrosion.
Alarm Logs and Sensor Failures
Most modern engineering systems come with integrated monitoring and diagnostic features. Alarm logs that flag cooling unit errors, such as “high temp alert” or “fan speed failure,” should never be ignored.
These logs are early indicators that the system is detecting performance issues before they become critical. Faulty sensors can also give false readings or fail to trigger alarms at all, which creates a false sense of security.
Regular sensor calibration ensures that readings are accurate and alerts are reliable.
A consistent review of diagnostic logs and sensor health can highlight patterns of failure and help schedule timely maintenance before failures become visible or damaging.
Preventive Measures: What You Can Do Now
To avoid unexpected cooling unit failures, implementing a preventive maintenance strategy is essential. Start by establishing a regular inspection schedule that includes cleaning filters, inspecting for corrosion, checking for leaks, and verifying sensor accuracy.
Use thermal imaging cameras to detect heat buildup that may not be visible to the naked eye.
Regularly monitor energy consumption trends and compare them to operational baselines to spot inefficiencies early.
Install redundant cooling units or backup systems in mission-critical environments to provide an extra layer of protection.
Training your technical team to identify early warning signs such as temperature fluctuations, unusual noise, and system alerts will also improve responsiveness.
Lastly, keep detailed maintenance records to track patterns and predict future servicing needs. This approach not only extends the life of your equipment but also ensures that operations run smoothly, safely, and efficiently.
Conclusion
Engineering cooling units are the backbone of thermal management in high-performance systems, from industrial machinery to electronics infrastructure.
When these units begin to fail, the signs are usually clear rising temperatures, abnormal noises, fluctuating readings, shutdowns, leaks, and energy spikes.
Each of these indicators points to an underlying issue that, if left unchecked, can lead to major equipment damage, downtime, and increased operational costs.
Understanding these failure signs allows maintenance teams and operators to act quickly, resolve issues early, and prevent system-wide failures.
Proactive monitoring, routine cleaning, coolant checks, and sensor calibration are all essential components of an effective cooling unit maintenance plan.
Rather than waiting for a system breakdown, engineers should treat temperature control as a constant priority.
Maintaining efficient cooling is not just about comfort or basic function it’s about safeguarding performance, reducing long-term costs, and ensuring uninterrupted operations in demanding environments.
Early detection and proper maintenance are the most reliable strategies to keep cooling systems running at peak efficiency.
Recognize the signs, respond accordingly, and the cooling unit will continue to perform when it’s needed most.