Underground environments are some of the most challenging spaces to work in. Whether it’s a mining site, tunnel project, or underground parking lot, these spaces are confined, poorly ventilated, and pose unique risks to workers and equipment.
One of the most critical systems for ensuring safety and efficiency in these settings is the underground ventilation system.
Without proper ventilation, harmful gases like carbon monoxide, methane, and hydrogen sulfide can accumulate to dangerous levels, while oxygen levels can drop below the threshold needed for safe operations.
Additionally, underground spaces can experience rapid temperature increases and high concentrations of dust, further endangering workers and machinery.
An underground ventilation system is designed to combat these hazards by ensuring a continuous supply of fresh air, expelling contaminated air, and maintaining optimal temperature and air quality.
Underground Ventilation System Key Components Explained
This article will break down the key components of these systems, explaining how they work together to create a safer, more efficient underground workspace.
Whether you’re an engineer, project manager, or simply curious about these systems, this guide will provide a clear, practical understanding of what makes underground ventilation systems essential.
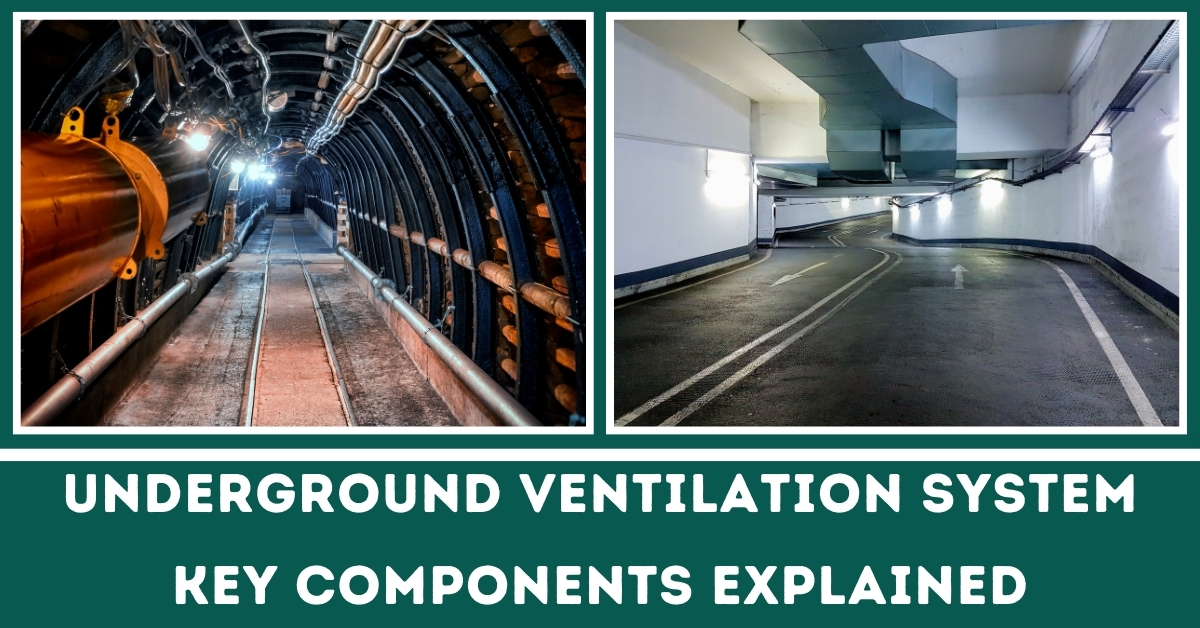
Why Underground Ventilation Matters
The underground environment is inherently risky. Oxygen levels can drop, harmful gases can accumulate, and temperatures can rise rapidly. Without effective ventilation:
- Carbon monoxide from equipment exhaust can reach hazardous levels.
- Methane in mining environments can create explosive risks.
- Workers face long-term exposure to dust particles, leading to respiratory issues.
The job of a ventilation system is to maintain safe air quality, regulate temperature, and provide a consistent airflow throughout underground spaces. This is accomplished through a combination of components working together.
1. Air Intake and Fresh Air Shafts
Air intake systems are responsible for bringing fresh air into the underground environment. These shafts or tunnels are strategically placed at the surface and connect directly to the underground site.
- Purpose: The primary function of air intake shafts is to supply fresh air to underground workspaces. Without these systems, oxygen levels would quickly drop, making it hazardous for workers.
- Key Features: Air intake shafts are often fitted with grilles and filters to prevent debris, insects, and other contaminants from entering the ventilation system.
- Optimization: The location of air intake shafts is planned to maximize airflow efficiency and ensure even distribution across the underground site.
2. Air Exhaust and Return Air Shafts
Air exhaust systems work in tandem with air intakes by removing contaminated or used air from the underground environment.
- Purpose: These shafts are crucial for expelling harmful gases such as methane, carbon monoxide, and dust particles that accumulate during operations like drilling and blasting.
- Design: Return air shafts are designed to channel used air back to the surface, often using large ducts or tunnels.
- Ventilation Balance: Proper placement and sizing of return air shafts ensure a balanced airflow, preventing stagnant or unventilated areas.
3. Fans and Blowers
Fans are the driving force behind any underground ventilation system, ensuring a continuous flow of air through the network.
- Types of Fans:
- Axial Fans: Commonly used for high-volume, low-pressure airflow. These are ideal for moving air over long distances.
- Centrifugal Fans: Suitable for high-pressure applications, such as removing heavy dust or gases.
- Placement: Fans are often installed at air intake points, exhaust shafts, or strategic locations within the underground space to maintain optimal airflow.
- Power Supply: Most fans are powered by electricity, with backup generators to ensure functionality during power outages.
4. Ventilation Ducts
Ducts are used to direct airflow within the underground system, ensuring air reaches all required areas.
- Materials: Common materials include galvanized steel, aluminum, and reinforced fabric, each selected based on the specific conditions of the underground environment.
- Flexibility: Flexible ducts are often used in dynamic operations like tunneling, where airflow requirements may change as the project progresses.
- Sealing: Proper sealing of ducts is critical to prevent air leakage and maintain the efficiency of the ventilation system.
5. Air Quality Sensors and Monitoring Equipment
Continuous monitoring of air quality is essential to ensure a safe working environment.
- Types of Sensors:
- Gas Detectors: Monitor levels of harmful gases such as methane, carbon monoxide, and hydrogen sulfide.
- Dust Monitors: Measure particulate concentrations to prevent respiratory hazards.
- Oxygen Sensors: Ensure that oxygen levels remain within safe limits.
- Automation: Modern systems are equipped with automated alerts that notify operators of unsafe conditions, allowing for immediate corrective action.
6. Cooling and Heating Systems
Underground environments can experience extreme temperatures, making temperature control systems a necessary component of ventilation.
- Cooling Systems:
- Designed to combat heat generated by machinery and geological conditions.
- Common cooling methods include chilled water systems, evaporative coolers, and air-conditioning units.
- Heating Systems:
- Used in colder climates to maintain safe working temperatures.
- Heaters are typically integrated into the airflow system to distribute warm air evenly.
7. Dust Control Systems
Dust is a significant hazard in underground operations, posing both respiratory risks and fire hazards.
- Water Sprays: Often installed at critical points like drilling or blasting sites to suppress dust at the source.
- Dust Collectors: Industrial-grade systems that capture and filter dust from the air, ensuring cleaner airflow.
- Duct Design: Proper ductwork design minimizes the accumulation of dust within the system, reducing maintenance needs.
8. Explosion-Proof Equipment
Given the presence of combustible gases and materials, ventilation systems often incorporate explosion-proof components.
- Explosion-Proof Fans: Specially designed to prevent sparks, reducing the risk of igniting flammable gases.
- Sealed Electrical Components: Electrical systems within the ventilation network are designed to prevent sparking or overheating.
- Compliance: All components must meet stringent safety standards set by regulatory bodies.
9. Emergency Ventilation Systems
Emergency systems are a critical safeguard in underground environments, ensuring safety during accidents or equipment failures.
- Backup Fans: Ensure continued airflow during power outages or mechanical failures.
- Escape Routes: Ventilation systems often integrate with emergency exit paths, providing fresh air for safe evacuation.
- Gas Purging Systems: Rapidly expel hazardous gases in emergency situations to prevent explosions or suffocation.
10. Control Systems and Automation
Modern underground ventilation systems are equipped with advanced control systems to optimize performance.
- Centralized Control Panels: Allow operators to monitor and adjust airflow, temperature, and air quality in real-time.
- Automation: Automated systems use sensors and algorithms to maintain optimal conditions with minimal human intervention.
- Energy Efficiency: Smart controls reduce energy consumption by adjusting fan speeds and airflow based on real-time needs.
11. Maintenance and Inspection Systems
Regular maintenance and inspection are essential for the longevity and reliability of underground ventilation systems.
- Inspection Protocols: Periodic checks ensure that all components, including fans, ducts, and sensors, are functioning correctly.
- Maintenance Tools: Many systems are equipped with built-in diagnostics to identify and address issues before they become critical.
- Cleaning: Ducts and filters must be regularly cleaned to prevent blockages and maintain airflow efficiency.
12. Regulatory Compliance and Standards
All underground ventilation systems must comply with strict safety and environmental regulations.
- Air Quality Standards: Ensure that air contaminants remain within permissible exposure limits.
- Equipment Certifications: All components must be certified for underground use, particularly in hazardous environments.
- Audits: Regular safety audits are conducted to verify compliance and identify areas for improvement.
Conclusion
Underground ventilation systems are the backbone of safety and efficiency in confined spaces like mines, tunnels, and underground construction sites.
These systems work tirelessly to provide fresh air, remove harmful gases, control dust levels, and regulate temperatures.
Each component whether it’s air intake and exhaust shafts, powerful fans, ventilation ducts, or advanced monitoring equipment plays a vital role in maintaining a healthy and safe environment for workers and equipment.
With the integration of modern technologies such as air quality sensors, automated controls, and energy-efficient designs, these systems have become smarter and more reliable.
Emergency ventilation features and explosion-proof components further enhance safety, ensuring rapid responses to unexpected hazards.
However, regular maintenance, inspections, and adherence to strict regulatory standards are equally critical to keeping these systems functional and compliant.
By understanding the key components and their functions, operators and engineers can design and maintain ventilation systems that meet the unique demands of underground environments.
A well-planned and maintained system not only ensures the safety and health of workers but also improves operational efficiency, making it an indispensable part of any underground project.