Underground ventilation system safety is one of the most overlooked yet critical aspects of operating any mine, tunnel, or large subterranean facility.
While these systems run quietly in the background, they are the lifeline that ensures clean, breathable air for everyone working below ground level.
Without a well-maintained ventilation network, workers can be exposed to harmful gases, dust build-up, and fluctuating temperatures that can lead to serious health risks, equipment failures, or even catastrophic accidents.
Statistics from global mining and construction industries prove that neglecting routine inspections is one of the top reasons for costly downtimes and regulatory fines.
The good news is, with a clear, structured approach to inspections and maintenance, you can prevent unexpected failures, extend the life of your equipment, and stay compliant with safety standards.
Whether you’re a facility manager, safety officer, or underground supervisor, having a realistic checklist and maintenance plan helps you catch small issues before they grow into major problems.
Underground ventilation system inspection checklist and maintenance plan
In this guide we will explain how to create and follow a practical Underground ventilation system inspection checklist and maintenance plan that keeps your operations safe and efficient.
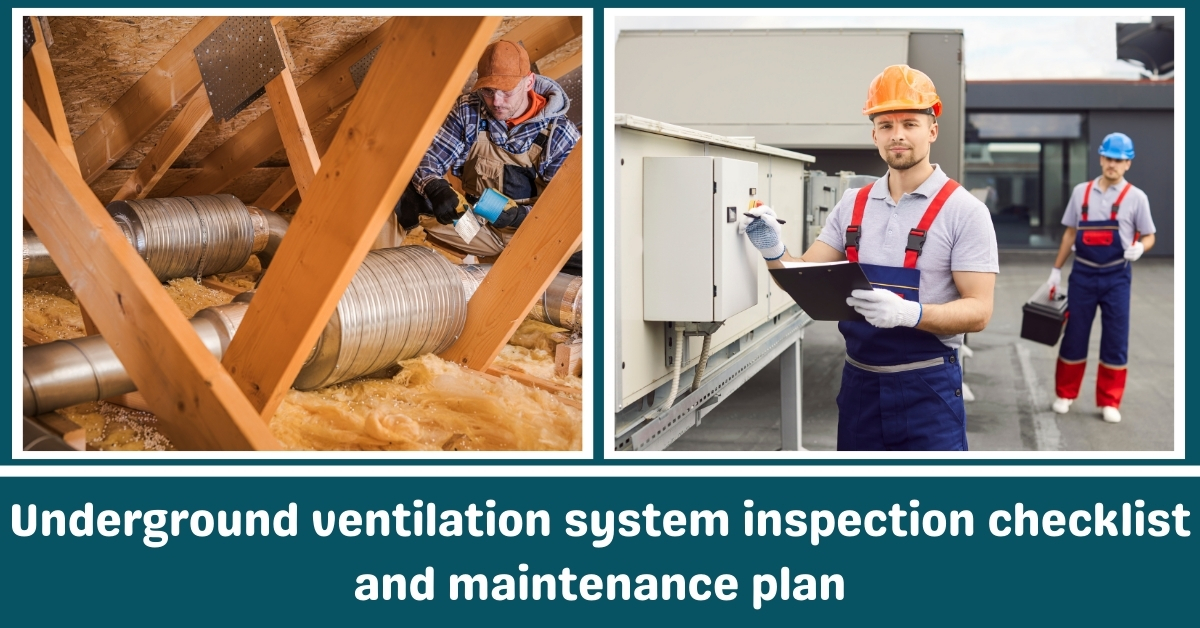
Why Underground Ventilation Demands Attention
A robust underground ventilation system is not just a regulatory requirement it’s a life-support network for any operation beneath the earth’s surface.
Underground work areas, whether mining tunnels, subways, or large basements, naturally accumulate gases like methane, carbon monoxide, radon, or diesel exhaust.
Without a steady supply of fresh air, these gases build up to dangerous levels, threatening worker health, equipment performance, and overall productivity.
Poor airflow can also cause heat and humidity to rise, which further endangers workers and damages machinery over time.
Regulatory bodies worldwide set strict standards for underground ventilation because even a minor lapse can lead to tragic outcomes.
Reliable ventilation helps control dust, remove contaminants, dilute and expel hazardous gases, and maintain a stable temperature.
Ignoring inspections and proactive maintenance allows small issues such as tears in ducts or a failing fan motor to snowball into bigger failures that can halt operations completely.
For these reasons, it’s critical to understand every component in your system, know how to inspect it, and build a routine that keeps air flowing safely underground.
Core Components of an Underground Ventilation System
A solid maintenance plan starts with knowing what you’re working with. An underground ventilation system has a few key elements that all work together to move fresh air in and push stale, contaminated air out.
First, you have primary ventilation fans, which are large, heavy-duty units that generate the main airflow through the entire underground network.
These fans often run 24/7 and must be reliable at all times. Next are secondary fans, which push air into specific sections like working faces, headings, or blind tunnels.
These can be smaller but play a crucial role in delivering fresh air right where it’s needed most. Ductwork comes next — this can be rigid or flexible, and it channels air to targeted areas.
Ducts must be airtight and properly supported so they don’t sag, tear, or disconnect.
Regulators, doors, and stoppings are barriers and gates that direct air where it should go, balancing flows throughout complex networks.
Many systems include air monitoring sensors that detect levels of gases, dust, or temperature to ensure conditions stay within safe limits.
Finally, any modern underground system should include emergency equipment like escape doors, fresh air bases, or refuge chambers, providing workers a safe zone if a ventilation failure or fire occurs.
Knowing where each of these components sits, how it works, and what can go wrong is the foundation for your inspections.
2. Underground Ventilation System Inspection Checklist
Inspections are only useful when they’re consistent and practical. A well-designed underground ventilation system inspection checklist breaks tasks into daily, weekly, monthly, quarterly, and annual steps. Daily inspections are frontline checks.
They should include measuring airflow with anemometers at key points to confirm it matches design requirements.
Gas monitors must be checked to ensure no buildup of methane, carbon monoxide, or other dangerous gases.
Primary and secondary fans should be observed for unusual noise or vibration, which could signal misalignment or worn parts. Emergency exits and safety chambers must be free of obstructions.
Weekly inspections should focus on more detailed fan checks: look at fan blades for buildup, belts for signs of wear, and motors for unusual heat.
Ducts should be visually checked for tears, leaks, or disconnections. Regulators and doors must open and seal properly to maintain correct airflow paths.
Dust accumulation should be monitored to prevent blockages. Monthly inspections require a full airflow survey across the entire system, comparing results to design targets.
This is also the time to check for corrosion on metal parts, apply protective coatings if needed, and inspect all electrical connections. Backup systems like emergency fans or generators should be tested.
Quarterly inspections dig deeper: performance trends should be analyzed, noise and vibration levels should be tested with proper tools, and all inspection records should be reviewed for accuracy.
Annual inspections should include a full system audit, ideally with a qualified external expert.
This is also when to plan for duct replacement in severely worn sections, check that the system meets current regulatory standards, and refresh staff training on ventilation safety procedures.
A routine like this keeps inspections clear, consistent, and easy to follow.
How to Build a Realistic Maintenance Plan
Having a checklist is only half the job making it work in real life means turning it into a repeatable plan. Start by assigning clear responsibilities for each task.
Daily checks can be done by operators who work underground every shift. Weekly and monthly tasks might fall to maintenance teams, while safety officers should oversee quarterly and annual reviews.
Next, create a practical maintenance calendar. Use software or even a wall chart to mark daily, weekly, and monthly tasks.
Add reminders for bigger audits and equipment replacement schedules. Keep this visible to everyone involved. Good record-keeping is essential: every inspection should be logged with date, time, what was checked, what was found, and what was fixed.
These records help identify recurring problems before they become emergencies. Include budgeting in your plan too.
Costs like duct replacement, fan motor overhauls, or new gas sensors should never be a surprise plan for them in your annual budget cycle.
Lastly, train your team. Even the best plan fails if your crew doesn’t know what to look for. Train everyone on spotting common faults, using measuring tools, and responding if ventilation drops below safe levels.
A realistic plan keeps everyone on the same page and prevents costly surprises.
Common Problems Found During Inspections (And Fixes)
Every underground ventilation system faces similar problems over time, and knowing what to expect can help you act fast. One of the most frequent issues is airflow obstruction.
This could be caused by debris buildup, collapsed ducting, or blocked regulators. The fix is straightforward: clear the obstruction, inspect the cause, and reinforce weak sections to prevent repeats.
Another common issue is damaged or leaking ducts. Tears or holes reduce airflow efficiency and can allow contaminants to recirculate.
Small tears can be patched with appropriate sealants; large damage means sections should be replaced. Corroded fans or ductwork happen where moisture and acidic gases are present.
The solution is to clean, treat, and apply corrosion-resistant coatings and replace badly rusted parts when necessary.
Sensor drift is another issue. Over time, gas or airflow sensors can become inaccurate. The best fix is regular calibration and timely replacement when they fail to hold accuracy.
Excessive vibration and noise in fans often point to misaligned shafts, loose parts, or worn bearings.
Vibration testing tools help pinpoint the cause; alignment checks and bearing replacements are standard solutions. Staying alert to these predictable problems makes your inspection work practical instead of reactive.
Benefits of a Strong Inspection and Maintenance Program
A consistent inspection and maintenance plan pays for itself many times over. First, it protects worker health and safety by ensuring the air they breathe underground is clean, properly circulated, and free of dangerous gas pockets.
It also guarantees compliance with industry standards, avoiding fines and potential shutdowns due to failed safety inspections.
Financially, a proactive plan keeps costs under control: it’s much cheaper to patch a small duct tear than to deal with a full system failure that stops operations for days.
Regular upkeep also extends the life of expensive equipment like primary fans and gas sensors, delaying costly replacements.
Moreover, a healthy ventilation system improves overall operational efficiency by keeping air at optimal flow rates, ensuring machinery operates within safe temperatures, and preventing dust buildup that can clog equipment.
Another overlooked benefit is worker morale when people feel safe underground, they’re more productive and less likely to raise health complaints.
In short, a good inspection and maintenance routine is a smart investment that protects people, profits, and peace of mind.
Sample Underground Ventilation System Maintenance Log Template
Keeping track of inspections is just as important as doing them. A simple log helps you prove compliance, spot patterns, and plan future repairs.
A good underground ventilation system maintenance log should have these basic columns: the date of inspection, type of inspection (daily, weekly, etc.), findings, action taken, and the inspector’s name.
For example, a daily entry might note that gas levels were within normal range, requiring no action. A weekly entry could record a minor tear in a duct, which was patched immediately.
A monthly entry might show a drop in airflow in one heading, prompting a deeper check that revealed a fan belt was slipping which was replaced.
Keeping this record up-to-date and accessible helps everyone stay on the same page. It also proves to regulators that you’re staying compliant with ventilation requirements.
Use paper logs, spreadsheets, or digital maintenance systems whichever works best for your team. The goal is to ensure nothing slips through the cracks and that every inspection and fix is traceable.
Conclusion
A dependable underground ventilation system is more than just an operational requirement it’s the backbone of safety, efficiency, and compliance in any underground environment.
When you take the time to follow a practical inspection checklist and stick to a realistic maintenance plan, you’re actively preventing small problems from becoming big, costly shutdowns.
You’re also protecting your team from exposure to hazardous gases, extreme temperatures, and poor air quality.
Staying organized with clear records, regular training, and a workable budget for repairs and replacements makes this entire process sustainable in the long term.
It’s not about adding unnecessary tasks it’s about creating daily habits that keep air flowing, equipment in good condition, and people safe.
Any underground operation that commits to a strong ventilation maintenance program will always be better prepared for unexpected challenges.
Use this guide as a foundation to build your own system that fits your site’s unique needs. Keep it clear, consistent, and practical and your underground operation will breathe easier every single day.