Warehouse cooling isn’t just about comfort it’s a critical operational need. As warehouse spaces grow larger and logistics become more complex, maintaining a stable, cool environment becomes increasingly difficult.
From product storage and preservation to worker safety and performance, temperature control impacts every aspect of warehouse management.
Yet, these buildings are often designed for function over form, with high ceilings, poor insulation, and constant foot and vehicle traffic that let heat in and trap it inside.
Add to that the heat generated from machinery, lighting, and summer sun, and you’re looking at indoor temperatures that can soar beyond safe working limits.
The result? Product damage, reduced productivity, increased energy bills, and potential health risks for staff.
Many warehouse operators rely on oversized HVAC systems that struggle to keep up or worse, ignore the issue altogether. But there are cost-effective, efficient solutions available that don’t require a complete building redesign.
Warehouse cooling challenges and how to overcome them
In this guide, we will explain the main challenges of warehouse cooling and provide practical, realistic strategies to overcome them.
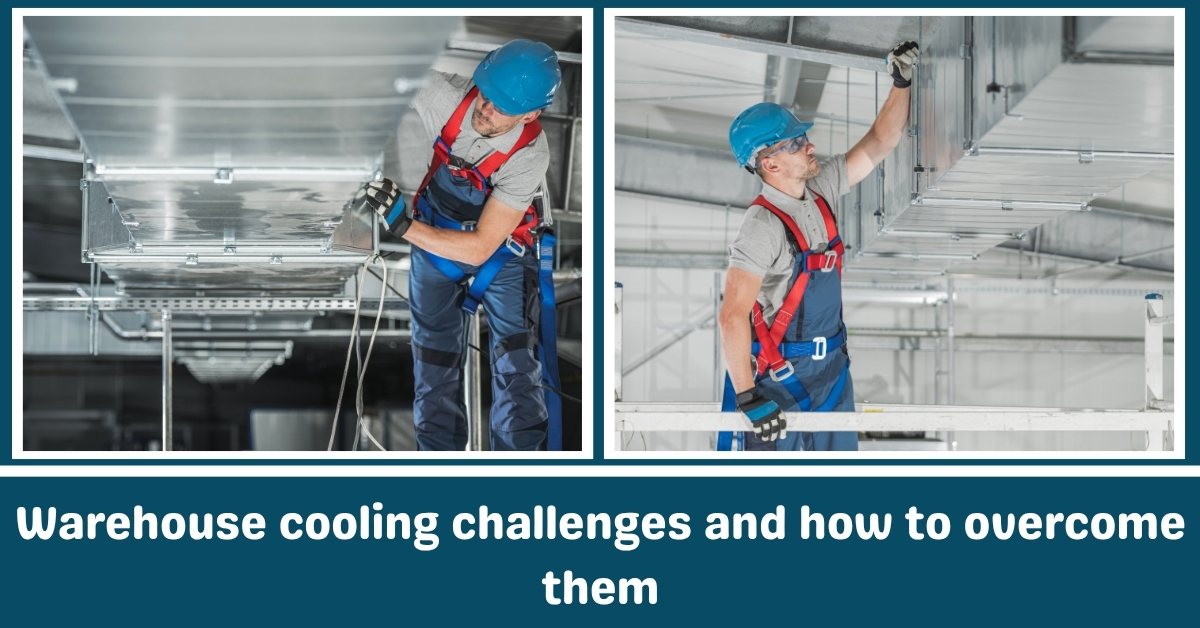
1. Understanding the Warehouse Cooling Challenges
Warehouses face several unique cooling challenges due to their design, usage, and environmental exposure. These challenges can affect not only the operational efficiency of a warehouse but also the safety of workers and the condition of stored goods.
One of the most significant issues is the size and structure of warehouses. These buildings are typically vast, with high ceilings and large open areas. They are built for storage and movement, not insulation.
The walls and roofs are often made of metal or concrete panels that absorb and retain heat, especially in the summer months.
Without proper insulation, these buildings heat up quickly and become difficult to cool, causing internal temperatures to rise significantly.
Another major challenge is the frequent opening and closing of large dock doors. Every time these doors open, hot outdoor air flows into the building, and cool air escapes.
In facilities with high shipping and receiving volume, this occurs dozens or even hundreds of times a day, making it nearly impossible to maintain stable temperatures.
In many warehouses, doors are left open for extended periods for operational reasons, which only worsens the heat issue.
Additionally, machinery used in warehouses—such as forklifts, conveyors, packaging equipment, and sorting machines—generates heat throughout the day.
Even the lighting in older warehouses can contribute to internal temperature rise, especially if fluorescent or halogen lights are used. This added heat further strains any existing cooling efforts and makes the air in the building feel heavy and stagnant.
Air circulation is another commonly overlooked problem. In large warehouse spaces, hot air tends to rise and remain trapped at ceiling level, while cooler air stays low.
Without an efficient system to mix and circulate air, hot zones develop, particularly in upper rack areas and enclosed corners.
Poor air circulation also means humidity can build up, increasing discomfort and damaging goods such as paper, cardboard packaging, or food products.
Employee safety and comfort are also at stake. High indoor temperatures can cause fatigue, dehydration, and even heat stroke.
According to OSHA, when warehouse temperatures exceed 80°F (27°C), productivity begins to drop, and risk to worker health increases. At higher thresholds, companies may face compliance issues or even shutdowns in extreme heat conditions.
Finally, energy consumption is a growing concern. Cooling a large building with inefficient equipment or poor layout leads to high electricity costs.
Attempting to cool the entire warehouse with traditional HVAC systems is not only expensive but often ineffective. These systems are rarely designed to handle the size and open nature of a warehouse, which leads to uneven cooling and wasted energy.
Understanding these challenges is the first step to improving warehouse cooling. The good news is that these issues can be managed through a combination of building upgrades, airflow management, and smarter cooling techniques.
2. How to Overcome Warehouse Cooling Challenges
Solving warehouse cooling problems requires a practical and multi-layered approach. Rather than relying on just one method like installing air conditioning, success comes from addressing the source of the heat, improving insulation, and enhancing air movement.
Below are the most effective strategies to improve cooling in a warehouse environment.
Step 1: Improve Building Insulation and Seal Entry Points
Start by examining the building envelope. Poor insulation allows heat to penetrate during the day and remain trapped overnight.
Adding reflective roof coatings and thermal insulation to walls and ceilings can reduce internal heat gain. In addition, inspect and seal all dock doors, loading bays, windows, and wall joints to prevent hot air from entering and cool air from escaping.
Weatherstripping and dock shelters are simple tools that make a significant impact in reducing external heat entry.
Step 2: Install HVLS (High-Volume, Low-Speed) Fans for Air Circulation
Air movement is essential in large spaces. HVLS fans are designed to push large volumes of air gently and consistently, creating steady airflow throughout the warehouse.
These fans don’t lower the actual temperature, but they do reduce the perceived temperature by up to 10°F (6°C), making the environment more comfortable for workers.
They are particularly effective when combined with other cooling methods, helping to distribute air evenly and prevent hot zones.
Step 3: Use Zoned Cooling Systems for Targeted Relief
Instead of trying to cool the entire warehouse, focus cooling efforts on areas where people work or where heat-sensitive products are stored.
Zoned cooling can be achieved by using portable air conditioners, ductless mini-split systems, or creating partitioned work zones with dedicated cooling.
This approach saves energy and reduces costs by cooling only where it’s necessary, without wasting resources on empty or low-priority areas.
Step 4: Integrate Evaporative Cooling Systems
In dry climates, evaporative coolers (also known as swamp coolers) are a low-cost and effective option. These devices work by passing warm air over water-saturated pads, cooling it before distributing it into the space.
They are simple to install and operate, use less energy than air conditioning, and are highly effective in open spaces. However, they are not suitable for humid regions, as they add moisture to the air.
Step 5: Upgrade to Smart Climate Control Systems
Installing programmable thermostats and automated cooling systems can improve efficiency. Smart systems can monitor temperature changes in real time and adjust fans or cooling units based on demand.
They can also run cooling systems during off-peak hours, reduce unnecessary energy use, and notify managers when conditions fall outside safe or desired levels.
Step 6: Switch to LED Lighting and Minimize Internal Heat Sources
Replacing outdated lighting with LED fixtures significantly reduces internal heat output. LEDs generate less heat than traditional fluorescent or halogen bulbs and consume less power.
Additionally, where possible, isolate heat-generating equipment or use barriers to reduce the spread of heat into common areas.
Step 7: Create Break Zones and Encourage Hydration
Protect your team by setting up rest zones with fans or portable air conditioning, especially in peak summer months. Ensure easy access to cold drinking water throughout the warehouse.
Encouraging regular breaks and hydration not only keeps workers safe but also maintains productivity levels.
Step 8: Perform Regular Maintenance on All Cooling Systems
Poorly maintained fans, air conditioners, or evaporative coolers can lose up to 30% of their efficiency. Clean filters, inspect motors, and check ductwork regularly to ensure everything runs at peak performance.
Establish a maintenance schedule and train staff to identify early signs of system inefficiency.
By combining these approaches, warehouse managers can create a more comfortable, energy-efficient, and productive environment without relying on expensive or high-maintenance systems.
3. Bonus Tips – Advanced and Cost-Saving Options
Once the basics of warehouse cooling are in place, additional upgrades can provide long-term savings and enhanced performance.
These advanced strategies may require more investment but can offer significant returns over time.
Step 1: Install Solar Panels to Offset Cooling Costs
Warehouses typically have large, flat roofs—ideal for solar energy systems. By installing solar panels, facilities can generate their own electricity to power cooling systems, lighting, and other equipment.
This reduces reliance on the grid and lowers electricity bills. In some regions, rebates or tax incentives can make the investment even more cost-effective.
Step 2: Apply Heat-Reflective Paints and Floor Coatings
Coating the roof and exterior walls with reflective paint can reduce the amount of heat absorbed by the building. Similarly, light-colored or reflective floor coatings reduce heat retention inside.
These upgrades work passively to maintain cooler temperatures and reduce the load on cooling equipment.
Step 3: Use Exhaust Fans and Roof Vents to Expel Hot Air
Installing exhaust fans at ceiling level and passive roof vents can help remove trapped hot air, especially during hot afternoons.
As hot air rises, these systems push it out, allowing cooler air to enter from lower openings or vents.
This natural ventilation technique is simple and effective, especially when paired with HVLS fans to support airflow.
Step 4: Install Thermal Energy Storage Systems
For facilities with high energy use or those operating in regions with time-of-use electricity pricing, thermal energy storage offers an advanced solution.
These systems cool water or other mediums at night when power is cheaper and use that stored cooling during the day. This helps flatten energy demand and reduce peak-time consumption.
Step 5: Redesign Layout for Better Airflow
Sometimes, rearranging storage racks or workstations can improve airflow. Avoid stacking inventory directly against walls or blocking ventilation paths.
Leave space between shelving units to allow air to move freely. If possible, align aisles in the direction of fan airflow to maximize circulation.
Step 6: Schedule Operations to Minimize Heat Exposure
Operational adjustments can also improve cooling. Consider scheduling heavy work or machine use during cooler hours of the day, such as early morning or late evening.
Limit dock door openings during peak heat hours and automate door closures where possible to reduce heat exchange.
Conclusion
Warehouse cooling doesn’t have to be complex or expensive it just needs to be strategic. By understanding the unique challenges posed by large, open, and poorly insulated spaces, you can begin to take targeted actions that deliver measurable results.
Simple upgrades like improving insulation, installing HVLS fans, and using zoned cooling systems can significantly reduce indoor temperatures and energy consumption.
For more advanced needs, solar panels, reflective coatings, and smart climate controls can further enhance performance and cost-efficiency.
Rather than relying solely on traditional HVAC systems which are often costly and ineffective in large spaces a layered approach combining air movement, insulation, ventilation, and operational adjustments delivers far better results.
Protecting your workers, preserving your products, and reducing your energy bills are all achievable when cooling strategies are planned carefully and executed with purpose.
The key is to start with what you can control and build from there. Even small improvements can make a big difference when applied consistently.
A cooler warehouse means a safer, more productive, and more sustainable operation overall.