Air conditioning systems play a crucial role in modern football stadiums and training facilities. These systems are responsible for maintaining optimal indoor temperatures, improving air quality, and ensuring comfort for players, staff, and thousands of spectators.
Unlike residential or small commercial HVAC setups, football field air conditioners operate on a much larger scale, often spanning multiple zones and handling extreme loads during peak events.
Without regular maintenance, these systems can become inefficient, prone to breakdowns, and significantly more expensive to operate.
Routine maintenance isn’t just about keeping the air cool it’s about ensuring consistent airflow, avoiding costly repairs, meeting safety regulations, and extending the lifespan of high-value equipment.
Skipping even basic upkeep can lead to higher energy bills, poor performance, and uncomfortable conditions that can impact player performance and fan experience alike.
Whether you’re managing an enclosed stadium, a semi-open arena, or a dedicated training ground, knowing what to inspect and when can save both time and resources.
Football field air conditioner essential maintenance checklist
In this guide, we will explain the essential Football Field Air Conditioner maintenance checklist you need to follow to keep your system running efficiently all year round.
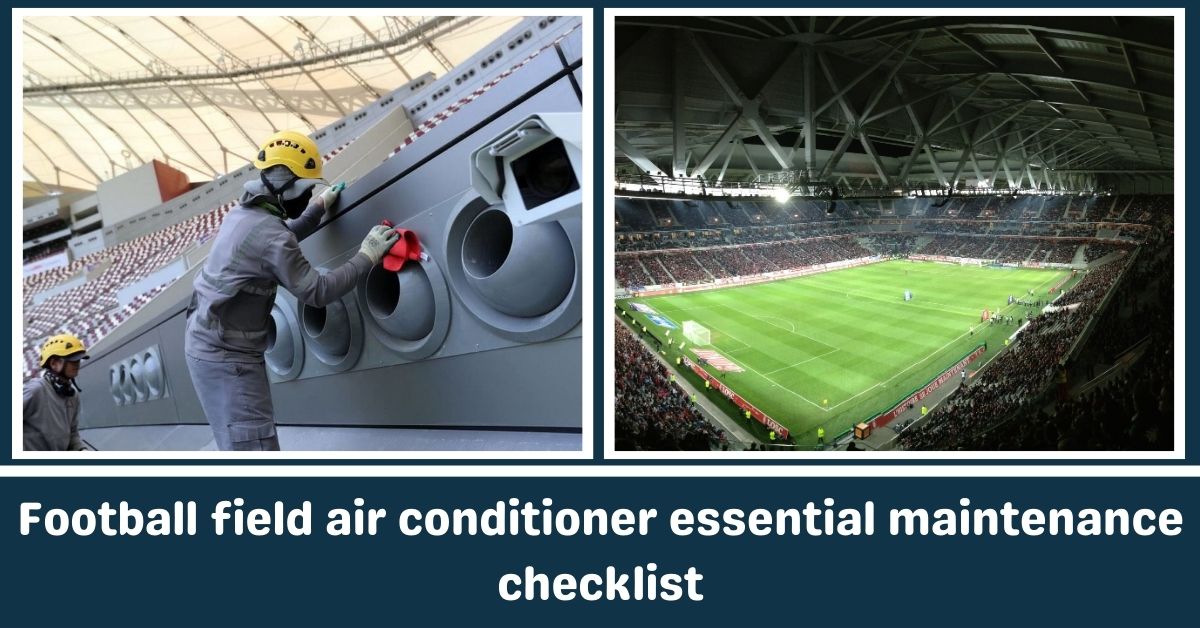
1. Why Maintenance Matters
Maintaining the air conditioning system in a football stadium or training facility is critical for ensuring reliable operation, energy efficiency, and occupant comfort.
These systems are often large, complex, and subject to high demand during matches and events. If not properly maintained, they can become inefficient, overwork the equipment, and eventually fail when needed most.
Without regular attention, issues such as clogged filters, refrigerant leaks, electrical faults, and mechanical wear can develop unnoticed until they lead to significant system downtime or costly repairs.
Regular maintenance helps keep energy costs under control. An air conditioner operating with dirty coils or low refrigerant levels can use 20–30% more energy than a properly maintained system.
It also improves system longevity; components like compressors and motors are expensive to replace, but with timely lubrication, filter changes, and inspections, their lifespan can be significantly extended.
Most importantly, stadium AC systems affect health and comfort.
Poor indoor air quality caused by lack of maintenance can lead to humidity problems, unpleasant odors, and even mold growth, which is especially problematic in crowded environments.
For players and spectators, clean, properly cooled air is essential for safety and performance.
2. Essential Maintenance Checklist
The essential maintenance checklist for football field air conditioning systems is divided into categories based on the frequency of tasks. Performing these regularly helps detect problems early and prevents unplanned outages.
Daily Checks:
Basic visual and functional inspections should be done daily, especially during the season.
This includes checking that thermostats are set correctly, confirming there are no unusual noises coming from equipment, and ensuring vents are not blocked.
Any signs of water leakage near air handlers or indoor units should be addressed immediately. Taking quick temperature readings in different zones helps spot imbalances or underperformance.
Weekly Checks:
Each week, maintenance staff should inspect air filters and change them if they show signs of clogging or if the pressure drop is above manufacturer recommendations.
Inspect drive belts for tension and signs of cracking. Clean the area around outdoor units to maintain proper airflow.
System operating pressures should be reviewed and compared against baseline data to ensure the unit is functioning within its designed range.
Monthly Checks:
Every month, coil cleaning should be done to remove dust and debris buildup that hinders heat transfer. Condensate drain lines and pans should be flushed and cleaned to prevent overflows.
Lubrication of motor bearings and moving parts is also recommended. Technicians should check refrigerant levels and verify there are no leaks, as low refrigerant reduces cooling performance and can damage compressors.
Electrical connections inside control panels should be inspected for loose terminals or discoloration that might signal overheating.
Duct insulation should be examined to ensure there are no tears or gaps, as this can affect thermal efficiency.
Quarterly Checks:
Every three months, conduct an air balance test using anemometers to ensure airflow is evenly distributed across all zones. Verify duct static pressure using manometers and check against system design specs.
Sensors connected to the BAS should be tested to confirm accurate readings.
For systems using UV lights in the air handling units, inspect the lamps and replace them if they’re reaching end of life.
Semi-Annual Maintenance:
Twice a year, deeper maintenance is needed. Fully clean condenser and evaporator coils using appropriate cleaners and water rinses. Perform a full inspection of the compressor, including amp draw comparison and short-cycle behavior.
Test the economizer function if the system includes one dampers should open and close correctly, and actuators must respond accurately.
Review all maintenance logs for the past six months to spot recurring issues or parts that may need replacement.
Annual Maintenance:
Once a year, schedule a comprehensive system review. This includes a shutdown/startup sequence, thermal imaging of electrical panels, and refrigerant leak testing with detection tools.
Calibrate thermostats and environmental sensors. Conduct duct cleaning if air quality reports or visual inspection reveal contamination.
Review system performance data to identify inefficiencies, such as higher energy usage per cooling ton than expected. Replace worn or aged components as needed to prevent breakdowns during peak season.
3. Documentation and Compliance
Proper documentation is a critical part of HVAC maintenance, especially in facilities as complex as football fields and stadiums. Every inspection, repair, and service activity should be recorded in a maintenance log, whether digital or physical.
These logs serve multiple purposes. First, they help technicians track the system’s condition over time and spot patterns of wear or failure. Second, they provide proof of compliance with manufacturer warranty requirements.
Many equipment warranties are only valid if regular maintenance is performed and documented.
Documentation is also important for safety and legal compliance. In many regions, systems that contain more than a certain quantity of refrigerant (typically 50 pounds or more) must be checked for leaks annually and reported to regulatory authorities.
Failing to do so can lead to fines. In addition, logs help stadium facility managers plan budgets for replacements or upgrades and provide a record in case of HVAC-related complaints or insurance claims.
Using a Computerized Maintenance Management System (CMMS) makes it easier to manage these records.
CMMS platforms can track maintenance schedules, create digital service logs, and generate alerts when a task is due. They also make it easier to assign responsibilities and track technician performance.
4. Red Flags to Watch For
Even with a solid maintenance schedule, some warning signs may appear between service intervals. Knowing what to look out for can prevent small issues from becoming major failures.
One common red flag is uneven cooling across different areas. If some sections of the facility are much warmer or colder than others, it could point to blocked ducts, a failing zone damper, or poor airflow.
Another issue is unusual sounds like banging, screeching, or buzzing, which may indicate loose components, worn bearings, or electrical problems.
Frequent short cycling where the system turns on and off rapidly is another indicator of potential trouble. It could mean the system is oversized, or that there’s a problem with the thermostat, sensor, or control system.
Rising energy bills without a corresponding increase in usage is also a clue that the system is running inefficiently, possibly due to dirty coils, low refrigerant, or poor airflow.
Excess humidity or condensation issues indoors may signal that the AC is not dehumidifying properly, often due to coil or airflow problems.
Water leaks, especially near air handlers or from the ceiling, should never be ignored. These often come from clogged drain lines or failed condensate pumps.
Finally, any electrical smell or the sight of burn marks on panels or wires requires immediate shutdown and inspection. These are serious fire hazards and could indicate overloaded circuits or deteriorating electrical connections.
5. Tips for Off-Season Maintenance
Off-season periods, when the facility is not hosting events or matches, offer a perfect opportunity to perform deeper maintenance tasks and prepare for the next active period.
One of the first tips is to run the system at least once a week, even during downtime. This prevents stagnation in coils, keeps components lubricated, and discourages mold growth in ducts.
Use the time to perform full system shutdown inspections, which may not be possible during the active season.
This includes deep cleaning of all air handling units, tightening electrical connections, verifying motor performance, and inspecting ductwork thoroughly for leaks or damage.
Inventory management is another useful task during the off-season. Restock air filters, belts, lubricants, and any spare parts that are regularly used. This ensures that the team is ready for any issues once the system is in full operation again.
Training is another smart investment. Use this quieter time to refresh the skills of in-house maintenance staff. Reviewing updated manufacturer manuals, safety procedures, and new diagnostic tools helps maintain service quality throughout the year.
Finally, review the year’s maintenance logs, performance metrics, and repair history. Identify patterns, such as repeat component failures or rising repair costs, which may indicate the need for a system upgrade or redesign.
Plan large-scale capital improvements like replacing outdated air handling units or installing energy monitoring systems, so they’re completed before the next high-demand period begins.
Conclusion
Maintaining a football field air conditioning system is not just a routine task it’s a vital responsibility that ensures consistent performance, energy efficiency, and comfort for players, staff, and spectators.
These systems operate under high demand and cover large areas, making proactive maintenance essential to avoid unexpected breakdowns, reduce energy waste, and extend equipment life.
From daily checks like monitoring airflow to annual inspections involving refrigerant testing and system calibration, every step in the maintenance checklist plays a specific role in keeping the system running smoothly.
Proper documentation and regulatory compliance are equally important, as they help track system health over time and ensure alignment with safety standards.
Identifying red flags early, such as unusual noises or uneven cooling, can prevent small issues from turning into costly failures. Off-season periods offer valuable opportunities for in-depth servicing and planning upgrades.
By following a structured maintenance plan and staying vigilant year-round, stadiums and training facilities can maximize HVAC system reliability and performance.
In the long run, a well-maintained air conditioning system supports a safer, more efficient, and more comfortable environment for all.