Tunnel construction presents a range of environmental and occupational challenges, with underground air quality ranking among the most critical.
As excavation progresses deeper below the surface, natural airflow is significantly restricted, creating an enclosed environment where heat, humidity, dust, and toxic gases can accumulate rapidly.
Without effective air conditioning and ventilation systems in place, worker health and safety are at risk, and project timelines can be severely impacted.
The air within a tunnel is influenced by several factors, including diesel engine emissions, blasting fumes, dust from rock cutting, and even geothermal heat.
These hazards require a combination of mechanical ventilation, cooling, and air purification to keep the environment within regulated safety standards.
It’s not just about comfort it’s about ensuring that every worker can breathe clean air and operate machinery efficiently.
Choosing the right air conditioning methods for tunnel construction depends on the project size, depth, geology, and ambient climate.
From forced ventilation to localized spot cooling and advanced chilled water systems, each method plays a role in keeping the underground workspace safe and operational.
Tunnel construction air conditioning methods to manage underground air quality
In this guide, we will explain the most effective tunnel construction air conditioning methods used to manage underground air quality.
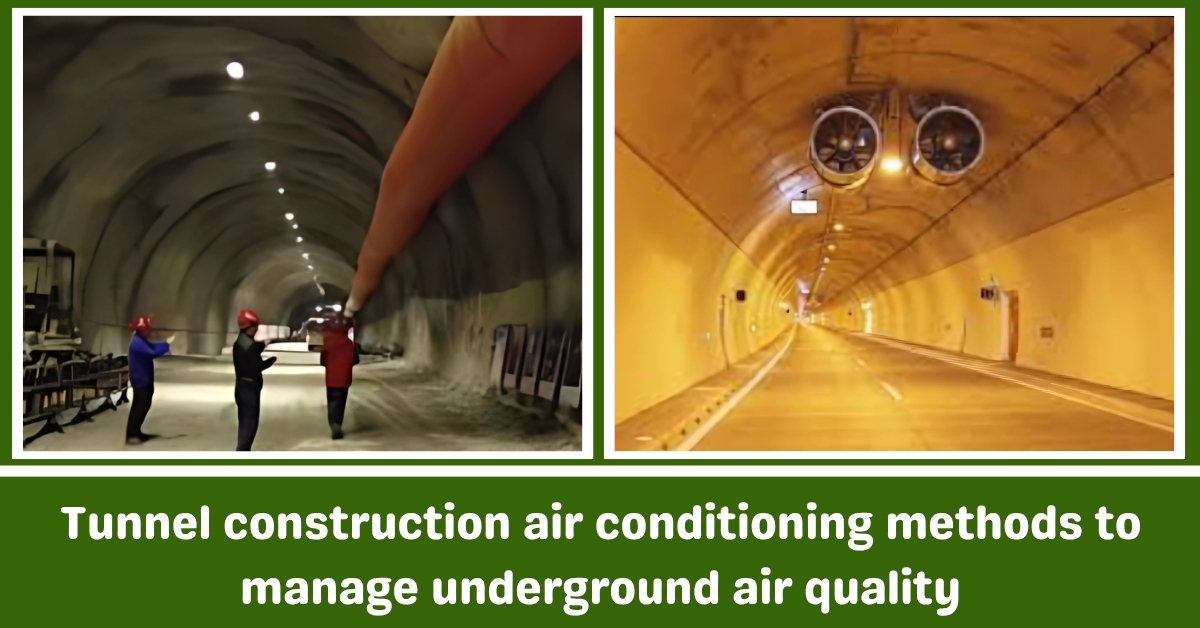
1. Why Air Conditioning in Tunnel Construction Is Essential
Tunnel construction creates a unique environment where natural airflow is limited or entirely absent. As excavation proceeds, the concentration of heat, moisture, dust, and harmful gases increases.
Air conditioning systems are essential because they ensure that workers can breathe safely and operate effectively in confined spaces.
Diesel-powered equipment, commonly used in tunnel works, releases carbon monoxide (CO), nitrogen dioxide (NO₂), and diesel particulate matter (DPM), all of which can pose serious health risks.
Explosives and drilling activities add to the pollution, and without a controlled air system, these pollutants build up to hazardous levels.
Additionally, underground temperatures can rise due to geothermal heat and friction from machinery.
When not managed properly, excessive heat and humidity can reduce worker performance, damage equipment, and delay operations.
Air conditioning plays a critical role in reducing temperature, removing moisture, and ensuring that harmful gases are diluted and extracted.
It also helps prevent structural damage by maintaining optimal humidity levels. In short, air conditioning is not optional it is a safety requirement in modern tunnel construction.
2. Key Objectives of Tunnel Air Conditioning
The main goal of tunnel air conditioning is to provide a safe, breathable, and comfortable working environment underground.
This involves controlling several environmental variables that affect both human health and machine performance.
First, maintaining adequate airflow is critical. Air movement helps in distributing fresh air and pushing out stale, polluted air. This ensures the entire tunnel, especially the tunnel face, is ventilated continuously.
Second, air conditioning helps in the removal of toxic gases and dust. Tunnel works generate a mix of particulates and combustion gases. Removing these substances quickly reduces the risk of respiratory problems, explosions, and equipment failure.
Third, controlling temperature and humidity is essential. High temperatures can cause fatigue and increase the risk of heat stroke.
High humidity accelerates corrosion and degrades construction materials. Air conditioning systems are used to stabilize these conditions.
Finally, air conditioning also aims to improve visibility and reduce condensation, which can impact safety and construction quality.
Meeting all these objectives ensures compliance with health and safety regulations while maintaining productivity.
3. Core Air Conditioning Methods in Tunnel Construction
Tunnel air conditioning involves various techniques and systems, each tailored to meet specific environmental and operational needs.
One of the most common methods is forced ventilation, where large axial flow fans blow fresh air into the tunnel through flexible ducts. This system is straightforward and widely used in shorter tunnels or early-stage excavations.
In contrast, exhaust ventilation systems operate by extracting contaminated air from the tunnel, allowing fresh air to enter naturally or through another duct system.
These systems are ideal where harmful gases need to be removed quickly, such as in blasting zones.
The push-pull system combines both supply and exhaust methods, creating a continuous cycle of fresh air inflow and contaminated air outflow.
This system is effective in longer or deeper tunnels, where simple forced ventilation is not sufficient.
Chilled water systems are used when heat and humidity levels are extremely high. These systems circulate chilled water to air handling units (AHUs) that condition the tunnel air.
They are commonly used in deep urban or hydropower tunnel projects.
Spot cooling units provide localized cooling at specific high-heat areas like the tunnel face or machine operating zones. These units can be portable air conditioners or evaporative coolers and are used to supplement general ventilation.
Evaporative cooling systems, which cool air through water evaporation, are useful in dry climates. These systems are low-cost and efficient where humidity is not already high.
Each method is selected based on tunnel length, depth, environmental conditions, and regulatory requirements. Often, a combination of these systems is used to achieve optimal air quality.
4. Equipment Used in Tunnel Air Conditioning
Various specialized equipment types are used to support air conditioning in tunnel environments. Each plays a specific role in achieving clean, cool, and breathable air underground.
Axial flow fans are the primary source of mechanical airflow. They are capable of delivering high air volumes over long duct distances. These fans are usually installed at tunnel portals or shafts.
Flexible ventilation ducts carry fresh air into the tunnel and direct polluted air out. These ducts are made of durable materials and can be extended or shortened as the tunnel progresses.
Dust filters and particulate collectors are integrated into air intake systems to prevent dust from recirculating. This is especially important in dry or heavily excavated zones.
Chillers are used in chilled water systems to produce cold water. These are typically installed at the surface and connected to a piping network that circulates to air handling units.
Air handling units (AHUs) control air temperature and humidity by conditioning the air before it enters the tunnel. They are often installed at key entry points or along the tunnel route.
Gas detectors and monitoring sensors are critical for safety. They measure levels of CO, NO₂, oxygen, and dust particles in real time. These devices inform when airflow needs to be adjusted or when emergency ventilation is required.
Humidity and temperature sensors help track environmental conditions and optimize cooling settings.
Each of these components is selected and maintained to match the specific conditions of a tunneling project.
5. Best Practices for Effective Tunnel Air Conditioning
Achieving efficient tunnel air conditioning requires more than installing fans and ducts. It demands a well-planned, responsive system that adapts to the changing conditions inside the tunnel.
Start with airflow modeling, using computational fluid dynamics (CFD) simulations to plan how air should move through the tunnel. This helps determine the optimal location of fans, ducts, and exhaust points.
Next, ensure regular maintenance of equipment. Ducts should be checked for leaks, fans for performance degradation, and filters for clogging. Chillers and AHUs should be inspected for water leaks and corrosion.
Use real-time monitoring. Install gas detectors, temperature sensors, and pressure gauges to track conditions constantly. Data from these devices allows for automatic adjustments to airflow and cooling.
Adjust systems as tunneling progresses. As the tunnel advances, duct lengths must be extended, and new fan positions must be calculated. Keep the system dynamic, not static.
Train workers on emergency ventilation procedures. Everyone should know what to do if gas levels spike or if ventilation equipment fails.
Incorporate redundancy into critical systems. Always have backup fans and power sources available to prevent shutdown during failure.
Following these practices ensures that air conditioning remains effective throughout the project’s life cycle.
6. Common Challenges and Solutions
Tunnel air conditioning systems often face practical challenges, especially as the construction environment changes. Understanding these issues helps in planning ahead and reducing downtime.
Duct damage is a frequent issue due to machinery movement and harsh conditions. Use reinforced or flexible ducts and protect them with support structures.
Overheating of fans in enclosed areas can lead to shutdowns. Install fans in ventilated areas and use water misting systems if necessary to reduce motor temperatures.
High power consumption can strain project budgets. Use energy-efficient fans and variable speed drives to adjust airflow based on need.
Water accumulation in ducts can cause corrosion and microbial growth. Install drainage points and use water-resistant materials.
Uneven air distribution may occur in long or branched tunnels. Use CFD modeling and install balancing dampers to ensure uniform airflow.
Temperature spikes near hot work zones like welding areas can affect surrounding workers. Use local spot cooling to isolate high-heat zones.
Addressing these issues early with planned solutions keeps air systems running smoothly and reduces health and safety risks.
7. Regulatory Guidelines and Standards
Tunnel air conditioning systems must comply with occupational health and safety regulations to ensure legal and safe operations.
In the United States, OSHA sets permissible exposure limits (PELs) for toxic gases such as carbon monoxide and nitrogen dioxide. It also mandates ventilation in confined spaces.
MSHA provides ventilation standards for underground mining operations, including airflow requirements and air quality monitoring.
In Europe, EN 12101 specifies design and performance criteria for smoke and heat ventilation systems used in tunnels.
Australia and New Zealand follow AS/NZS 1715, which deals with respiratory protection and air quality limits.
Local environmental and construction authorities may also require routine air quality assessments and approvals before certain operations.
All air conditioning systems in tunnel projects should be reviewed against relevant regulations to ensure full compliance. Failure to do so can result in work stoppages, penalties, or worker health incidents.
8. Future Trends in Tunnel Air Conditioning
Advancements in technology are shaping the future of tunnel air conditioning. Emerging trends focus on efficiency, automation, and sustainability.
IoT-based monitoring is gaining traction. Smart sensors connected to centralized systems allow for real-time control of ventilation and cooling. This ensures quick responses to changing air conditions and minimizes energy use.
Energy recovery ventilation (ERV) systems are being explored. These recover heat or cooling energy from exhaust air and use it to pre-condition incoming air, reducing power consumption.
Modular and portable cooling units are becoming more common. These allow for flexible deployment, especially in projects where conditions change frequently.
Hybrid systems combining traditional ventilation with renewable energy sources like solar power are being tested to reduce the environmental impact.
Lastly, AI-based predictive maintenance tools are being developed to detect wear and inefficiencies in fans, chillers, and ducts before failure occurs.
These trends indicate a move toward smarter, greener, and more responsive tunnel air conditioning solutions in the years ahead.
Conclusion
Effective air conditioning in tunnel construction is not just a matter of comfort it is a core element of safety, operational efficiency, and regulatory compliance.
Underground environments expose workers to a combination of heat, humidity, dust, and harmful gases, all of which must be carefully controlled to maintain a safe working space.
Whether it’s forced ventilation, exhaust systems, chilled water cooling, or spot cooling units, each method plays a distinct role in managing air quality depending on the tunnel’s length, depth, and surrounding conditions.
A successful tunnel air conditioning strategy involves more than equipment installation. It requires thoughtful planning, real-time monitoring, regular maintenance, and an adaptive approach as the tunnel advances.
Integrating air conditioning systems with broader ventilation plans ensures that workers can breathe safely and perform tasks without interruption or risk.
As tunnel projects grow more complex, adopting advanced technologies like IoT sensors and energy-efficient systems will become increasingly important.
These solutions not only enhance air quality management but also reduce long-term operational costs.
Ultimately, prioritizing underground air conditioning isn’t an optional upgrade it’s a vital requirement that supports the health, productivity, and success of any tunnel construction project.